Understanding Level Switches: Types, Applications, and Benefits – Explore the various types of level switches, their applications in industries like oil & gas, chemical processing, and water treatment, and the benefits they offer for maintaining safety and efficiency in industrial processes.
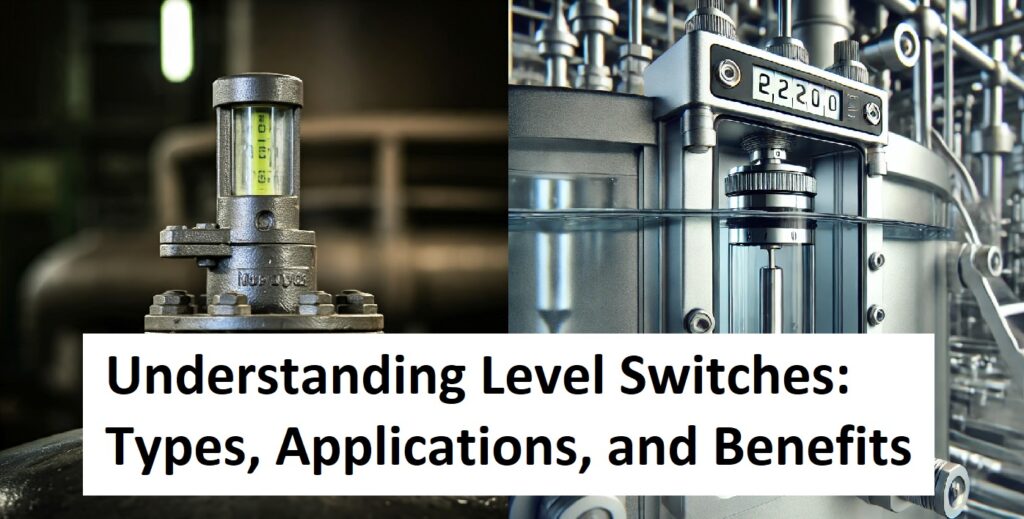
Understanding Level Switches: Types, Applications, and Benefits
In various industrial processes, maintaining accurate and consistent levels of liquids, solids, or gases in containers is crucial. Level switches are essential devices designed to detect the level of materials within tanks or vessels and ensure optimal operational efficiency and safety. This post will explore what level switches are, their types, and how they are used in different industries.
What is a Level Switch?
A level switch is a sensor that detects the presence or absence of a material at a specific level in a container or tank. When the material reaches a pre-determined level, the switch sends a signal to a control system, which can trigger alarms, start or stop pumps, or even activate specific machinery. This helps prevent overflow, run-dry conditions, or inconsistencies in material storage.
Types of Level Switches
There are several types of level switches available, each suited for different applications and materials:
- Float Level Switch
One of the most common and simple designs, float switches use a buoyant object that rises and falls with the liquid level. When the float reaches a certain point, it actuates the switch. These are often used for liquids like water, oils, and chemicals. - Capacitive Level Switch
These switches work by detecting changes in capacitance caused by the presence or absence of a material between the sensor and a reference electrode. Capacitive level switches are ideal for detecting liquids, powders, or granular materials, even in challenging conditions. - Optical Level Switch
Using light beams to detect the presence of liquids, optical level switches are often used in small, confined spaces. They work well with clear or semi-clear liquids and are resistant to external factors such as vibrations and mechanical wear. - Vibrating Fork Level Switch
This type of switch has two vibrating prongs that change frequency when submerged in liquid or solid material. It’s commonly used for applications with fine powders, granular materials, or liquids that might otherwise stick to surfaces. - Conductive Level Switch
Conductive (or conductive point) switches use the electrical conductivity of the liquid to trigger the switch. They are perfect for detecting conductive liquids, like water, and are widely used in chemical and wastewater treatment plants.
Applications of Level Switches
Level switches are versatile and used across numerous industries, including:
- Oil & Gas: Detecting oil levels in storage tanks and pipelines.
- Chemical & Petrochemical: Monitoring tank levels of hazardous chemicals and controlling fluid handling processes.
- Food & Beverage: Ensuring consistent liquid levels during production and preventing overflow in storage vessels.
- Water Treatment: Maintaining proper levels in reservoirs and ensuring safe water storage in tanks.
- Pharmaceuticals: Managing liquids during production to maintain strict hygiene and process control.
Benefits of Level Switches
- Safety: By preventing overflow or tank overfilling, level switches help reduce safety hazards and environmental risks.
- Efficiency: Level switches allow for automated control of processes, reducing manual intervention and improving productivity.
- Cost-Effectiveness: With proper monitoring, level switches reduce downtime caused by equipment failures due to low or high-level conditions.
Home | Join us on Facebook, Twitter, YouTube, Instagram, Quora, Reddit, LinkedIn, Pintereset, Blogger.